Invited Lecturer
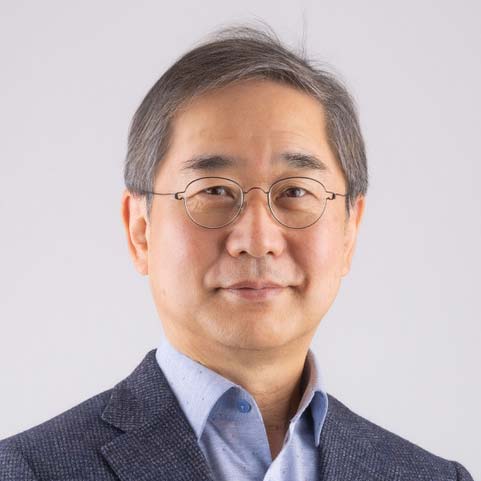
Prof. Ho Jang
Korea University
Tailoring the static and dynamic friction coefficients to reduce brake noise
Brake noise generated during braking is triggered by stick-slip at the sliding interface. To reduce the noise propensity of a brake system, therefore, research efforts have focused on minimizing the stick-slip amplitude, which is determined by the difference between static and dynamic coefficients of friction. Common strategies to reduce stick-slip amplitude rely on minimizing the difference by material design with the knowledge of the stick time-dependent static friction coefficient and velocity-weakening dynamic friction coefficient. Based on the key features of the two friction coefficients, a methodology for reducing the energy that triggers brake noise is presented, with emphasis on the effects of the composition of the brake friction material and the grey iron disc, which together determine the real contact area at the sliding interface.
He is a Professor Emeritus of Materials Science and Engineering at Korea University. He has performed friction materials research for 31 years and published more than 100 papers on the friction and wear of brake friction materials and discs in peer-reviewed journals. He carried out research projects to improve the brake performance for automobile manufacturers (Hyundai Motor Company, Ford Motor Company, Hyundai Mobis, HL Mando) and friction material companies (Sangsin Brake, Saeron Automotives, KB Autosys, Hongsung Brake Inc.) using his fundamental understanding of friction, wear, and friction-induced vibration. He also performed more than various government-funded research projects to study the fundamental mechanisms of friction induced phenomena. He is currently a member of the advisory board of Asia Brake and SAE Brake Colloquium and a steering committee member of the International Friction Forum. In 2018, he was awarded the Dan Mahannah Achievement Award from SAE International for distinction and significant contributions to the brake and friction material industries.
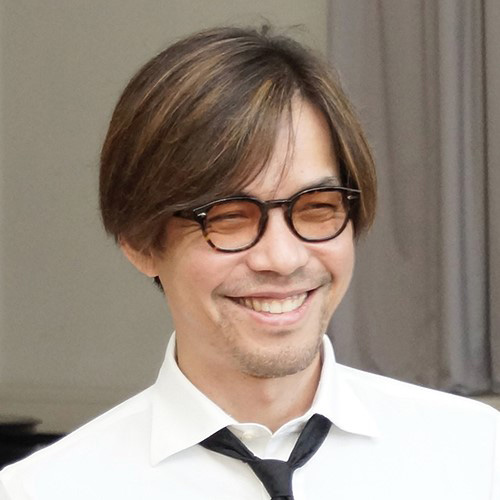
Prof. Dr. Ken Nakano
Yokohama National University, Japan
Does solid viscoelasticity stabilize sliding systems?
When analyzing the stability of a sliding system, we usually assume a friction law. By investigating the dynamics of a physical model using the friction law, we obtain mathematical stability conditions that serve as system design criteria for steady sliding. However, sliding systems are built not only from a mechanical point of view but also from a material point of view. In the above traditional approaches, the material properties of the sliding material are always invisible and hidden deep within a mysterious dimensionless number: friction coefficient. Therefore, in this study, we utilize a physical model that does not require an explicit friction law. The used model, the Kelvin-Voigt viscoelastic foundation model, considers the friction force on a rigid probe in contact with a viscoelastic solid, which originates from the repulsive force between them. Through the analysis, we finally find that although the dampers in Kelvin-Voigt elements dissipate mechanical energy during the sliding process, the solid viscoelasticity does not necessarily stabilize the sliding system.
He is a full professor at the Faculty of Environment and Information Sciences of Yokohama National University. He studied aeronautics and astronautics at the University of Tokyo and obtained his doctorate from the University of Tokyo in 1997. After working as an assistant professor at Saitama University from 1997 to 2000 and as an associate professor at Yokohama National University from 2000 to 2015, he obtained a full professorship at Yokohama National University in 2015. His specialized field is tribology, especially the physics of friction. He published over 100 reviewed papers. He was a board member of the Japanese Society of Tribologists from 2017 to 2019. Since 2024, he has been an Editor of Tribology Letters, published by Springer Nature.
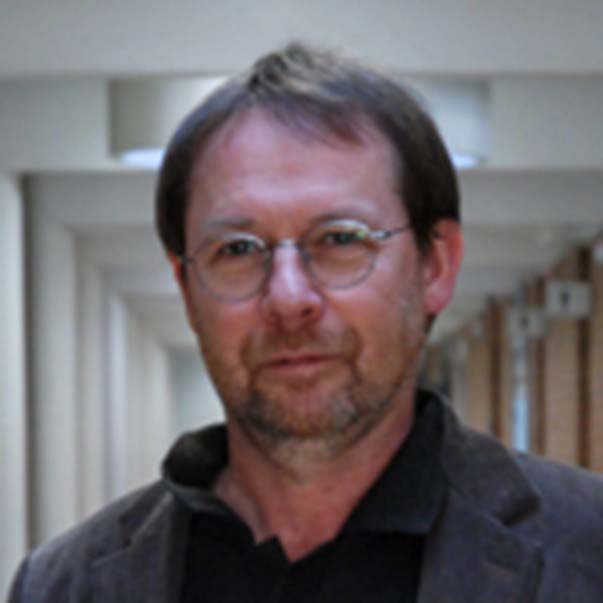
Prof. Dr. Yannick Desplanques
Centrale Lille, University of Lille
Particle Emissions as a Tracer of Processes at the Interface
The wear of friction brakes and the resulting PM emissions are major issues with regard to the environment and the materiel consumption of materials. Wear is usually approached through the prism of the wear mechanisms of friction materials. Quantification is based on losses in mass, thickness or volume, most often measured a posteriori, which limits identification and knowledge of the processes responsible.
Alternatively, wear can be defined by the material lost from the contact, i.e. the wear flow, according to the concepts of third body, tribological circuit and triplet introduced by M. Godet and Y. Berthier in the 80‘s and 90’s, particulate emissions being a part of it. From this end, their measurement in real time provides a dynamic tracer of wear mechanisms and their activation during braking. This presentation addresses the relationship between braking emissions and the tribological triplet and circuit on the basis of an example. Identifying emissions from wear processes provides keys to solutions for limiting emissions.
He is Professor Emeritus of Mechanics at Centrale Lille, University of Lille (France), and a member of the Laboratory of Multiphysics and Multiscale Mechanics. His main contributions concern fatigue, damage mechanics and failure analysis of materials, as well as tribology. His research work has focused on braking by friction for more than thirty years, in particular for railway transport. He has focused on the understanding of the tribological circuit and the role of the third body in energy dissipation, friction-induced vibrations and wear.
Industry Keynote
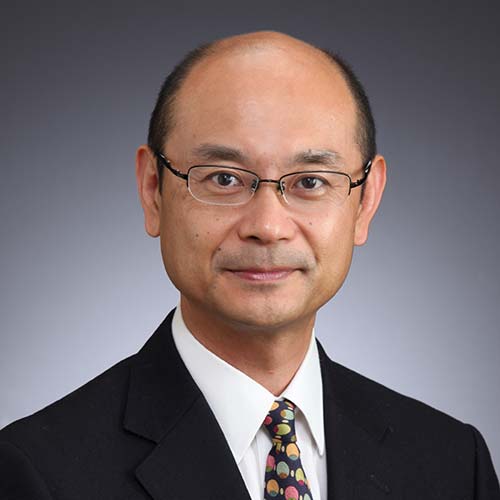
Toru Matsushima
Senior Staff Engineer. Chassis Development Div. No.2 Toyota Motor Corporation
Impact of Vehicle Electrification on Friction Brake Design
Due to the regenerative braking that appeared in the electrification of automobiles, the load on friction brakes has been greatly reduced.
The introduction of regenerative braking due to the electrification of vehicles has significantly reduced the load on friction brakes.
Regenerative braking not only improves fuel and energy efficiency but also reduces wear on pads and rotors, making it an excellent means to comply with regulations aimed at lowering brake particle emissions as specified by Euro 7.
Therefore, regenerative braking is a very important technology for braking to address environmental issues, and the proportion of regenerative braking used during braking is expected to increase in the future.
The reduction in friction brake load due to regenerative braking significantly alters the characteristics of friction couples, leading to various challenges such as noise and rust on the rotor friction surfaces. Consequently, there is a need for the development of new technologies to address these issues. In the development of friction couples, it is necessary to significantly review the design methods and testing methods for friction couples, which have been cultivated in internal combustion engine vehicles.
On the other hand, there is also the advantage that the durability of the rotor and pads is improved by reducing the friction brake load due to regenerative braking. It can also be considered that rotor surface treatment, which was not durable under the friction brake load of internal combustion engine vehicles, may be satisfied with durability in electric vehicles. Based on these findings, in this report, we will summarize the issues of friction brakes, which are greatly affected by the advent of regenerative braking, and consider the direction of friction brake design.
Responsible for technology development for brake noise and vibration reduction.
Specialized in experimental analysis of brake squeal and vibration and brake design technology development.
Joined Toyota Motor Corporation in 1984.
Belonged to the University of Michigan as a visiting scholar to research squeal analysis models in 1993-1994.
Received Doctor of engineering at Kyoto University in 2017.
Retired Project General Manager in 2022 and rejoined Toyota Motor Corporation as professional partner.
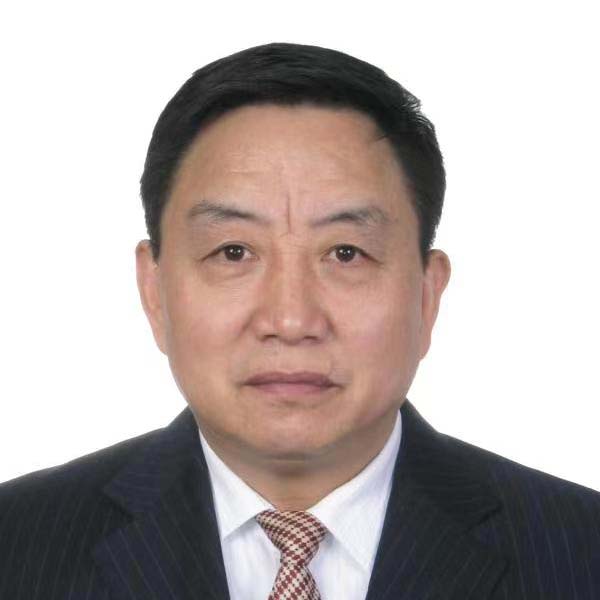
Wang Yao
China Friction & Sealing Material Association (CFSMA)
Introduction of Chinese brake product market
First, brake product industry profile
China is the world's largest brake product factory country, nearly 20 years, China's brake material industry has undergone tremendous changes, production capacity from small to large, from a single product to multiple varieties, from the original product imports to a large number of exports to more than 80 countries, and even for the international well-known automobile factory original supporting.
Production technology and equipment level from a relatively backward situation, to achieve leapfrog development, automation, intelligent equipment innovation and development and widespread use, improve the working conditions, stable product quality, improve labor productivity.
Second, brake product market capacity
China's automobile production, sales and ownership continue to grow, providing a huge consumer market for brake products.
Production and sales growth of new energy vehicles in China.
Number of fuel vehicles in China, number of new energy vehicles in China.
Prediction of the future development of China's automobile production and sales.
Chinese companies have moved production plants to avoid taxes, and international cooperation has increased opportunities.
He is currently the honorary president of CFSMA, the special Vice president of China Building Materials Federation, the vice chairman of China National Non-metallic Ore Standardization Technical Committee, the chairman of friction materials Sub-committee, and the member of the Advisory committee of Asian Brake Annual Meeting.
Graduated from Xi 'an University of Architecture and Technology, majoring in mineral processing, senior engineer, has worked in the National Non-metallic ore Research and Design Institute, Building Materials Trade Promotion Council and other institutions engaged in business and management work. Since 1999, he has presided over the comprehensive work of CFSMA and established the largest exhibition and exchange platform among international friction materials peers. In 2006, it cooperated with universities to hold undergraduate education on friction materials, and has so far trained more than 800 professional and technical personnel on friction materials. He has organized dozens of enterprises to go abroad to participate in international exhibitions and exchange activities; Invite dozens of international experts to hold technical lectures in China; Lead the Chinese brake pad enterprises for the United States three major automobile companies to achieve the original supporting.
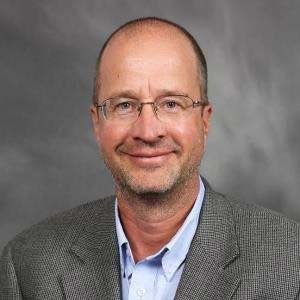
Rick Kaatz
Vice President and General Manager, KBAutosys America
Recent Developments in OEM Friction Materials – North America
Brake technology continues to evolve at a high rate of change. Electrification at the vehicle and brake component level, tighter fuel economy and emission requirements, and shorter development and validation cycles are some of the new challenges for friction material suppliers to deal with. An overview will be provided about the state of business in the US from a friction material supplier’s perspective.
Rick is Vice President and General Manager of KBAutosys America, an OE brake pad supplier headquartered in S. Korea.
He retired from General Motors in 2017 after 32+ years working in various brake engineering and management positions.
Rick holds Bachelor’s and Master’s degrees in Mechanical Engineering from Iowa State University and the University of Michigan.
Rick is chair of the Brake Linings Standards Committee, member Executive Committee and Technical Advisory Committee for the Brake Colloquium, and participates in several other SAE committees and task forces.
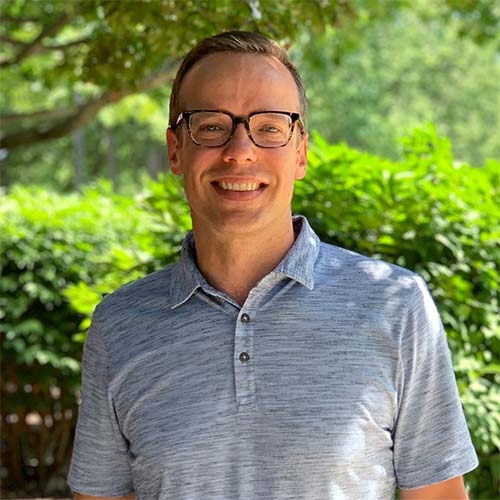
Adam Link
Vice President | Chief Technology Officer
Link Group, Inc. | Link Engineering Company
Evaluating variability, measurement uncertainty, and dynamometer capabilities for GTR 24 test facilities using interlaboratory testing
With the release of GTR 24 that is pushing laboratories across the world preparing to conduct the required testing and measurements, the industry has a common set of questions: What type of measurement uncertainty should I expect and how much variability exists across laboratories?
A study using a common reference brake assembly across multiple dynamometers and laboratories is performed utilizing recommended ISO standards. We examine Repeatability and Reproducibility for dynamic controls and outputs, including critical dynamometer control parameters and sampling air flows. We also attempt to provide a closer look into measurement uncertainty for torque, rotational speed, and KE using dynamic outputs.
Adam is the Chief Technology Officer, as well as Vice President of Link Group. He is responsible for the strategy, innovation, and technical leadership around all of LINK's businesses and is passionate about supporting LINK's customer base with innovative testing solutions.
Adam's previous roles have included leadership and technical positions that have resided both in the US and across Asia, including China and Korea. Starting as an Applications Engineer, he moved to roles including General Manager, Technical Director, and Managing Director. He has a Bachelor's in Mechanical Engineering and a Master's in Business Administration.
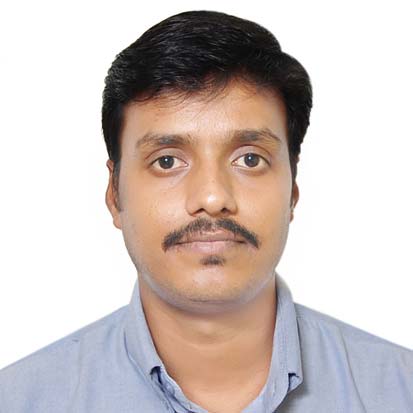
Karthikeyan A
Chassis Engineering Design Department 1 (CED-1-Suspension/Brake/Steering/Wheel&Tire), Head of Department, Hyundai Motor India Engineering, India.
The Impact of Electric and Hybrid Vehicles on Brake System Design
The increasing adoption of hybrid and electric vehicles (HEVs/EVs) is driving significant changes in brake system components design.
The unique characteristics of HEVs/EVs, including regenerative braking and high-torque electric motors, require brake system components that can efficiently manage heat, provide smooth and consistent braking performance, and integrate with advanced driver assistance systems (ADAS).
His presentation explores the impact of HEVs/EVs on brake system component design, including brake pads, rotors, calipers, and electronic control systems. It also discusses the challenges and opportunities presented by HEVs/EVs, including the potential for improved brake performance, reduced maintenance costs, and enhanced safety features.
Keywords: Hybrid and Electric vehicles, Regenerative braking, Advanced Driver Assistance Systems.
Karthikeyan A is the Head of the Chassis Department at Hyundai Motor India Engineering, a fully owned subsidiary of Hyundai Motor Company Group, South Korea.
With over 18 years of experience in chassis part development, including brakes, suspension, wheels & tires, and steering systems, he focuses on integrating these components with vehicle dynamics parameters to meet the design and performance requirements for Indian customers. He also represents HMC R&D, where he collaborates on future developments to ensure designs and performance meet the changing market requirements and demands.